Iron Ore - Beneficiating Low Grade Ores
Why it matters
The biggest
loser
In the mining industry, every tonne of ore counts. Our advanced beneficiation technologies recover potentially lost fine valuable iron ore into shippable product, ensuring no resources is wasted. This not only boosts profitability but also aligns with sustainable mining practices, reducing environmental impact and promoting resource efficiency.
The Challenge
No mineral
left behind
Low grade iron ore deposits often result in significant amounts of fine iron lost to tailings, impacting both economic returns and resource utilisation. These lost fines represent untapped potential, leading to inefficiencies and increased operational costs. Addressing this challenge is crucial for maximizing the value of mining operations and minimizing environmental footprint.
Mineral Technologies offers cutting-edge beneficiation technologies, including: MT Spirals, MT Reading WHIMS, MT Carrara HTR, MT Lyons Unit, and MT Modular Plants. MT solutions enhance metallurgical recovery, resulting in an extended lifespan of MT processing equipment and a long-term return on investment.
By integrating advanced engineering and metallurgical expertise, we help clients achieve superior efficiency and sustainability in their operations.
The Solution
Choose your
weapon
MT Spirals maximize iron ore recovery and efficiency with over 40 variants tailored to different minerals. Their robust, low-maintenance design ensures high separation efficiency and long service life.
The Reading WHIMS upgrades iron ore fines and recovers fine iron ore from tailings streams. It offers high efficiency and reduced operational costs, tailored to client needs.
The Lyons Unit stabilizes and controls feed density in iron ore processing, ensuring consistent slurry density and enhancing metallurgical performance.
FlexSeries modular plants combine high-quality spiral technology with advanced design, offering exceptional performance and reduced water consumption in iron ore processing.
2.6 Billion tonnes
In 2021, global iron ore production was estimated at 2.6 billion tonnes, a 4% increase from 2020.
>60% Grade
The operational focus was to optimise the separation circuit to recover high grade 66% Fe iron concentrate.
51 Billion tonnes
Australia holds the largest iron ore reserves, representing 28.3% of the world’s total reserve.
20% less cost
Compact and low weight construction reduces installation costs. No reagents are used in the circuits; this delivers environmentally friendly processes reducing operating costs and lowering potential for environmental incidents
MT specializes in flowsheet development through detailed ore sample characterization. This forms the foundation for a conceptual flowsheet, proven by metallurgical testing, supporting engineering studies, detailed design, and project development.
– Ed Hart
MT Iron Ore Specialist & Principal Metallurgist
What is Next
Sustainable and profitable future
Embrace a future where economic success and environmental responsibility align. Our beneficiation solutions boost profitability by improving ore recovery while supporting sustainable mining. By optimizing resources and minimizing waste, we help you meet business goals and contribute to a greener industry. Test your ore today and unlock its full potential.
Equipment
Proven results
Our latest range of equipment underpinned by decades of unmatched real world experience.
Brenda Van Rhyn
Regional Manager – Australia
Focus: Fine Minerals Recovery
I am a results-driven chemical engineer, passionate about delivering innovative equipment solutions that maximize revenue while minimizing costs.
The Expert
Reach
Out!
Ready to explore how our advanced solutions can revolutionise your operations? We’re here to help. Reach out to us today to learn more about how we can tailor our solutions to meet your specific needs and objectives.
Get detailed Insights
Success Stories
Chrome Spiral Replacement - Maximize Sustainable Performance
Why it matters
Chrome Spiral
into Recovery
As the global leader in chrome production, South Africa faces the pressing challenge of reliability in its fines processing operations. The industry demands robust equipment capable of enduring the abrasive nature of chrome extraction. Our advanced spirals excel in durability, efficiency, and reliability, outperforming competitors while maximising production in a smaller space. Embrace the future of chrome mining with our promise of enhanced longevity and profitability.
The Challenge
Tough on
Rough
Chromite processing faces many unique challenges arising from the high particle densities encountered, the erosive nature of the ore and the frequent presence of very fine particles that lead to clogging and reduced spiral efficiency. When these are combined with ore variations and product quality challenges an innovative approach to spiral design is needed to improve and maximise separation efficiency. Mineral Technologies embraces these challenges and produces the world-leading spiral designs you need for your operation.
Our Solution
MT Spirals
Our advanced spirals are engineered to provide consistent and reliable performance in chrome mining operations. Unlike traditional solutions that may falter under the abrasive conditions of chrome extraction, our spirals excel, offering unparalleled durability and efficiency. With our spirals, mining operators can trust in a reliable solution that minimises downtime and maximises productivity.
With over 40 spiral variations, speak to us about which spiral works for you, and kick things off with testwork in our own mineral lab.
Both our Australian and South African facilities are ISO 9001 certified.
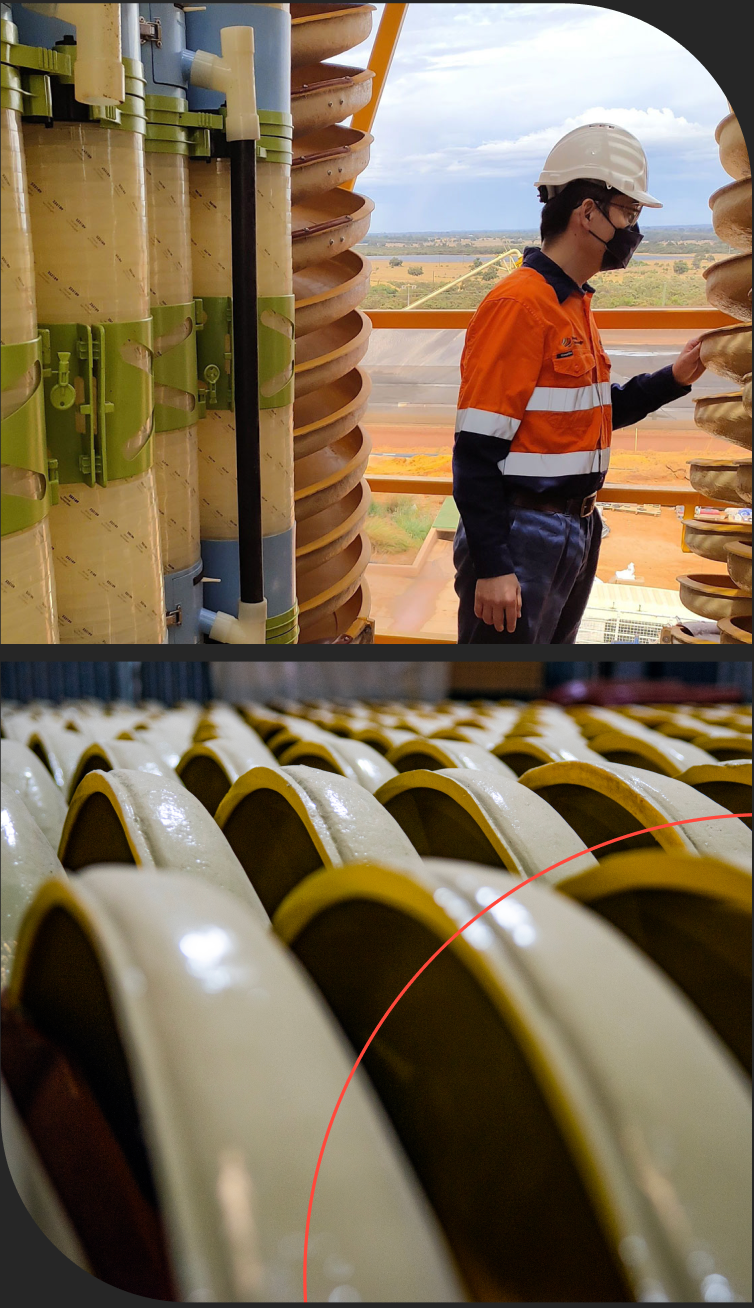
The Advantages
Less is more
Mineral Technologies is a well-established company with inhouse expertise in Met Services (laboratory and ore analysis). Our testing services will provide you with accurate and reliable information about the composition and properties of your minerals and how you get them best.
Every orebody is different. By analysing your ore samples, we can apply the most effective spirals and other proven MT separation technologies. Benefit from MT experts supporting you with guidance on how to optimise the performance of your plant.
Prevent downtime, reduce maintenance needs, and minimise repairs. In operations – reduce waste, increase yields, and lower operating costs. Testing your ore samples with Mineral Technologies can help you avoid costly mistakes by identifying potential issues with your current spiral separator setup.
Outperforming
Industry Standards
MT spirals offer superior chrome recovery with a compact design that consumes less space in mines. This advanced technology enhances efficiency and sustainability in mineral processing.
85%
Recovery Rate
15%
Average reduction in waste
<10%
Cr in tails
+1 Million
MT Spirals manufactured
The thing with chrome is: You want to extract something that wears down your equipment in the long run. So make it as strong as possible.
– Stephan Van Staden
Business Unit Manager Africa
What is Next
Spiral into
a sustainable
future
Our spiral solutions are more than just technological innovations—they are the keys to unlocking the full potential of chrome extraction. By maximising recovery rates, reducing operational costs, and ensuring durability in harsh mining environments, our spirals not only enhance profitability but also pave the way for sustainable mining practices. As the global demand for chrome continues to rise, it is imperative that we embrace solutions that not only meet current needs but also safeguard the future of the industry. We are not just mining chrome; we are shaping the future of chrome extraction for generations to come.
Equipment
Proven by results
Our latest range of equipment built by decades of unmatched real world experience.
James Agenbag
Fines Beneficiation Expert
Focus: Fine Minerals
I am a chemical engineer with two passions: physical separation and customers. Let’s solve your processing problems.
The Expert
Reach
Out!
Ready to explore how our advanced technology can revolutionise your operations? We’re here to help. Reach out to us today to learn more about how we can tailor our solutions to meet your specific needs and objectives.
Get detailed Insights
Success Stories
Mineral Sands Mining - Decrease Transport Cost Of Raw Feed Material
Why it matters
Driving
Profitability,
Sustainably
In mineral sands mining, transporting raw feed material is a constant challenge that impacts operational costs and environmental footprint. Addressing this issue is crucial for enhancing profitability while promoting sustainable practices.
The Challenge
Conventional
Constraints
Overcome
Traditional mining methods like truck-and-shovel operations are carbon-intensive, labor-intensive, and capital-intensive. They also pose risks of environmental degradation and community disruption due to expansive mining footprints and transportation requirements.
Solution
Mobile Mining Redefined
The Mobile Mining Unit (MMU) revolutionizes raw material transportation. This cutting-edge technology efficiently processes minerals on-site, eliminating the need for constant hauling between extraction and processing points.
- MMU Dry Feed – 750 TPH
- MMU Slurry Discharge – 42% solids
The Solution
Choose your
weapon
Unlock new revenue streams by extracting valuable minerals from tailings previously considered waste. This process generates additional income and reduces the need for new mining operations.
Recover and recycle up to 90% of process water, significantly reducing fresh water consumption. This is crucial in arid regions and helps preserve local water resources.
Process tailings on-site to eliminate the need for expansive tailings dams, reducing land use and mitigating the risk of dam failures.
Customise our approach with tailored process designs to maximise resource recovery efficiently, ensuring effective and economically viable solutions for each mining operation.
With decades of experience in tailings processing, our expertise ensures robust and effective solutions. Our successful projects worldwide provide confidence in our ability to deliver reliable outcomes.
Reduce energy usage, water consumption, and waste volumes, enabling more sustainable mining practices. This helps in reducing CO2 emissions and aligns with global sustainability goals.
50% Reduction
The MMU can reduce operating costs by up to 50% compared to traditional truck-and-shovel dry mining operations.
460 Million tonnes
The mineral sands industry alone extracts around 460 million tonnes of materials per year.
70% Less C02
The MMU technology can achieve up to 70% reduction in CO2 emissions compared to conventional dry mining methods.
$1.2 Billion
Extraction costs estimated at $1.2 billion annually.
What is Next
Sustainable Mining,
Resilient Future
Prioritize environmental stewardship while driving profitability. Our innovative MMU harmonizes resource extraction with sustainable practices, minimizing land use, water consumption, and carbon emissions, securing a resilient future for mining operations and local communities.
Equipment
Proven by results
Our latest range of equipment built by decades of unmatched real world experience.
Stephen Barnett
Product Manager – Mobile Mining Units
Focus: Pit to plant in shallow Soft Rock Mining
I am a results-driven Product Manager passionate about leading change and ensuring consistent delivery of business results.
The Expert
Reach
Out!
Ready to explore how our advanced Mobile Mining Unit can revolutionise your operations? We’re here to help. Reach out to us today to learn more about how we can tailor our solutions to meet your specific needs and objectives.
Get detailed Insights
Success Stories
Mineral Sands - Improvement Of Process Performance
Why it matters
Future proof
With over 80 years of expertise in high-yield, cost-effective, and sustainable mineral sands solutions. Our end-to-end services, from testing to support, include innovative technologies like our Spirals, Lyons Unit and WHIMS for efficient extraction of valuable minerals.
Committed to responsible mining, we strive to minimise environmental impact. Our approach maximises yield, future-proofs mines, and boosts investor confidence in sustainable, profitable mineral sands projects.
Approach
One stop shop
No two ore bodies are the same. Our process engineers begin with exploring and interrogating mineral sands processing solutions utilising testwork programs specifically designed to maximise the extraction of ilmenite, rutile, zircon and other fine minerals.
From our testwork we deliver concept, prefeasibility and feasibility studies as well as cost effective flowsheets to safely and efficiently extract the fine minerals. We then continue to work with customers through project lifecycles to deliver ongoing support and processing expertise to ensure project goals are achieved. The following figures are our benchmarks.
The Challenge
Latest mature technology
Marginal deposits and complex ores present formidable obstacles in mineral sands processing. Traditional methods often fall short, leaving valuable resources untapped and increasing environmental footprints. The industry grapples with rising costs, stringent regulations, and the pressing need for sustainable practices. Without innovative solutions, we risk missing out on critical minerals essential for green technologies and economic growth, while potentially causing unnecessary harm to our planet.
Our Solution
Proven precision globally
Our comprehensive approach revolutionises mineral sands processing. We offer a seamless journey from initial testing to plant design and operation, all under one roof. Our cutting-edge technologies, like the MG12 spirals and HTR400 separator, maximise recovery while minimising waste. By tailoring solutions to each unique deposit, we unlock the full potential of mineral sands, ensuring efficient extraction and processing. This not only boosts profitability but also reduces environmental impact, paving the way for a more sustainable mining future.
Equipment
Proven technology
Our latest range of equipment built by decades of unmatched real world experience.
Size
Matters
Total Global Production of Mineral Sands
Total Weight: 3.278 (Mt)
3,278,000
tonnes
21,853 Blue Whales
The equivalent of total mineral sands production.
9,832 Boeing 747s
The equivalent of total mineral sands production.
Customers value our ongoing commitment to researching and developing new, innovative equipment designs that extract maximum value from mineral sands deposits.
– Etienne Raffaillac
Principal Metallurgist
What is Next
Sustainable and Profitable Future
As we push the boundaries of mineral sands processing, we’re not just improving efficiency – we’re redefining responsible resource extraction. Our innovative solutions minimise land disturbance and water usage while maximising mineral recovery. This approach not only boosts profitability but also aligns with global sustainability goals. By partnering with us, you’re choosing a path that balances technological advancement with environmental stewardship, ensuring a brighter future for both industry and planet.
Brenda Van Rhyn
Regional Manager – Australia
Focus: Fine Minerals Recovery
I am a results-driven chemical engineer, passionate about delivering innovative equipment solutions that maximize revenue while minimizing costs.
The Expert
Reach
Out!
Ready to explore how our advanced technologies can revolutionise your operations? We’re here to help. Reach out to us today to learn more about how we can tailor our solutions to meet your specific needs and objectives.
Get detailed Insights
Success Stories
Relocate & Decrease Risk Of Tailings Dams
Why it matters
From Lose-Lose to Win-Win
Transforming Tailings Management with Profitable Solutions. Mining operations produce vast amounts of tailings, which can endanger communities and ecosystems if not managed responsibly. Proper stewardship of these waste streams is essential for environmental care and social responsibility. We’re here to help you turn this challenge into an opportunity. By reprocessing tailings as they are moved, you can not only reduce risks but also unlock additional revenue by recovering and selling valuable mineral products.
Together, we can shift from a lose-lose situation to a win-win approach, ensuring safety, sustainability, and profitability.
The Challenge
Mitigating
Catastrophic
Risks
The vast amount of tailings, often hundreds of millions of cubic meters, makes relocation costly and logistically challenging. Securing regulatory approval for new dams is increasingly difficult due to stricter safety and environmental rules, often taking years. Tailings dams remain a safety and environmental risk even after mine closure. Community consent and trust are also essential, as a lack of transparent engagement can lead to strong opposition and challenges in relocating facilities.
Our Solution
A future
not wasted
Our cutting-edge Mobile Mining Unit (MMU) transforms tailings from waste liabilities into valuable resources. By “slurrying” tailings and making them pumpable, the MMU enables efficient and safe relocation of tailings dams. The MMU’s advanced techniques and modular plant designs allow constantly transporting raw feed material from the extraction point to another location while minimizing environmental footprints.
This unique technical solution addresses the critical challenges of tailings management, reducing environmental risks and operational costs. Proven in various applications, the MMU is a game-changer for the mining industry, offering a sustainable and economically viable solution for tailings reclamation.
The Advantages
Less is more
The MMU allows for selective mining, minimising waste material and reducing the volume of tailings that need to be stored.
Remote operation of the MMU reduces human exposure to hazardous conditions near tailings dams.
The MMU pumps material through pipelines instead of using trucks, lowering the risk of accidents and spills.
Its mobility enables targeted extraction, avoiding environmentally sensitive areas and reducing waste.
High water recycling rates in MMU operations reduce the liquid content in tailings, decreasing the risk of dam failures.
The MMU produces fewer emissions and dust compared to traditional methods, contributing to a safer and cleaner environment.
What the
numbers say
715 High risk
The number of tailings dams that are classified as high to extreme risk.
4.4 Accidents
The number of tailing dams accidents each year.
$12 Billion in penalties
The estimated liability from fines for “High to Extreme Consequence” dams.
19 Catastrophic failures
Were predicted globally between 2018 and 2027.
Our step by step solutions combine proven expertise and separation technologies to minimise operational costs whilst processing tailings profitably.
– Stephen Barnett
MT Product Manager Mobile Mining Unit (MMU)
What is Next
Responsible Mining,
Resilient Future
De-risking communities and the environment while driving efficiency. Our solutions harmonise resource extraction with sustainable practices, securing a resilient future for mining operations and surrounding regions. By prioritising environmental and social responsibility, we ensure that mining activities contribute positively to both local communities and the global ecosystem.
Equipment
Proven by results
Our latest range of equipment built by decades of unmatched real world experience.
Stephen Barnett
Product Manager – Mobile Mining Units
Focus: Pit to plant in shallow Soft Rock Mining
I am a results-driven Product Manager passionate about leading change and ensuring consistent delivery of business results.
The Expert
Reach
Out!
Ready to explore how our advanced Mobile Mining Unit can revolutionise your tailing operations? We’re here to help. Reach out to us today to learn more about how we can tailor our solutions to meet your specific needs and objectives.
Get detailed Insights
Success Stories
Iron Ore - Tailings Dam Reclamation
Why it Matters
Maximising
untapped
potential
Vast quantities of iron ore tailings lie dormant, representing a significant untapped resource. Harnessing this potential is crucial for driving operational efficiency and sustainable mining practices.
Our Mobile Mining Unit (MMU) and FlexSeries, coupled with the MT Lyons Unit, provide mobile, scalable solutions for efficient mineral recovery from tailings, leveraging advanced technology for profitable and sustainable operations.
The Challenge
Chasing your
tailings
Reprocessing tailings with traditional methods is often uneconomical and environmentally taxing. Expansive tailings dams pose catastrophic risks, while truck-and-shovel operations are carbon-intensive and labor-intensive.
Mineral Technologies’ MMU and FlexSeries Modular Plant, enhanced with the MT Lyons Unit for consistent feed, enable efficient on-site extraction and processing from tailings, optimising resource recovery while minimising environmental impact.
Investing in this technology enhances profitability by converting waste to revenue, reducing disposal costs, and rapid setup and versatility for various sites, ensuring a quick ROI.
Our Solution - MT MMU
Replace
truck and
shovel
Our MMU represents the pinnacle of soft rock mining and tailings recovery. Designed to give you access to difficult locations, the MMU offers a sustainable and cost-effective solution.
Our Solution - MT Lyons Unit
For consistent
feed
The MT Lyons Unit stabilises slurry discharge in tailings dam reclamation, managing fluctuating inputs and enabling high-density pumping. This ensures consistent material flow for improved tailings management and more efficient reclamation processes.
Our Solution - MT FlexSeries
Efficient
on-site
extraction
The FlexSeries offers modular, customisable processing plants for tailings dam reclamation. It combines advanced spiral technology, reduced water use, and easy assembly, while minimising environmental impact and supporting efficient site restoration.
The Advantages
Less is more
Recover up to 70% more minerals from tailings stockpiles compared to traditional processing methods. Our advanced separation technologies ensure maximum resource recovery.
Our integrated systems feature a modular design that streamlines processes. These systems are also highly resource and energy efficient ensuring significant cost savings across the value chain.
Minimise land use, water consumption, and carbon emissions and reduce reliance on heavy machinery. Promote sustainable mining practices.
This integrated system offers adaptable configurations to suit various mining environments, ensuring optimal performance and cost-effectiveness across different operational scales. It allows for seamless deployment across multiple sites, adapting to your evolving operational needs with ease.
Finally we have found a solution which makes economical sense to reclaim the remaining grade from your dams.
– Leopoldo Bigarella
Regional Manager South America
What is Next
Zero harm
harmony
Prioritise environmental responsibility while driving profitability.
Our innovative tailings processing solutions harmonise resource extraction with sustainable practices, securing a resilient future for mining operations and local communities. By minimising land use, water consumption, carbon emissions, and waste volumes, we enable mining activities to align with global sustainability goals while unlocking new revenue streams from previously discarded tailings. This synergistic approach not only mitigates environmental risks but also enhances operational efficiency, driving profitability and long-term viability.
Through responsible resource stewardship, we empower the mining industry to contribute positively to local ecosystems, safeguard community well-being, and ensure the industry’s social license to operate, paving the way for a resilient and sustainable future.
Equipment
Proven by results
Our latest range of equipment underpinned by decades of unmatched real world experience.
Stephen Barnett
Product Manager – Mobile Mining Units
Focus: Pit to plant in shallow soft rock mining
I am a results-driven Product Manager passionate about leading change and ensuring consistent delivery of business results.
The Expert
Reach
Out!
Ready to explore how our technologies can revolutionise your tailing operations? We’re here to help. Reach out to us today to learn more about how we can tailor our solutions to meet your specific needs and objectives.